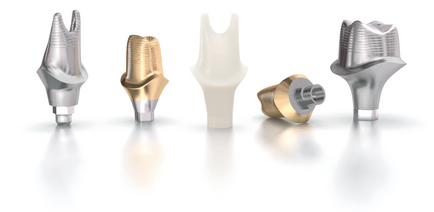
Today, dental implants are a standard part of a dental practice. They are reliable, predictable, and when designed properly, restorations seat easily. Dentists have the option to use a stock abutment, or a custom abutment designed specifically for the patient in question. Custom abutments designed via CAD/CAM (Computer-aided Design/Computer-aided Manufacturing) further enhance the process by providing a custom solution for each case with the final restoration in mind, giving proper tissue emergence and strength for the desired material choice. Before any of that is decided upon, however, the impression post and implant replica must be considered.
The challenge for dental labs doing implant restorations is lack of information. There are approximately 15 recognized implant companies in the U.S., and almost 200 companies worldwide making some type of dental implant. Many of these companies have their own connection type and parts, and many of these parts look alike. It is understandable that there would be some confusion when attempting to locate the correct driver or screw, or trying to determine which implant system it is just by looking at an impression post. Ordering the wrong part, or trying to find out which implant system it is can cost time and money for both parties.
Here are some practical steps that will insure success with every implant case:
Always communicate the type of implant system in its entirety. Many implant manufacturers have sub-categories. For example, Nobel Biocare Active vs. Nobel Biocare Replace. The surgeon who placed the implant will have this information in writing, which can be copied and sent with the prescription for the implant case to the lab.
Verify the platform size. Implant systems usually have three main measurements; the length, the implant size, and the platform size. The lab needs the platform size more than all other measurements. For example, an implant might be listed as a 3.8, when in fact the platform size is a 3.0. When in doubt, send all pertinent information.
When ordering an impression post/coping, also order the coinciding implant replica/analog at the same time. This saves the dental practice money and it saves the lab time, allowing the completed restoration to be returned sooner.
For implant cases covering 4 or more units, include a study/pre-op model or a diagnostic wax-up to ensure the lab achieves proper restoration placement.
Allow a minimum of 3 weeks for the lab to return the finished case. Implant cases take more time to process, as more steps are required.
These are suggestions for making implant restorations a reliable part of the dental practice. Parts can be challenging, given the number of systems available. Mountain Dental Lab, Inc. has implant lunch and learns that fit your schedule and can help you and your staff with identifying and ordering proper parts. We would be happy to schedule one of these for you – just give us a call at 828-665-2257 or email me at [email protected]. Our goal is to support you in what you do, because “We Love Being Part of Your Practice”!
Thank you for your time.
George Zoller, CDT